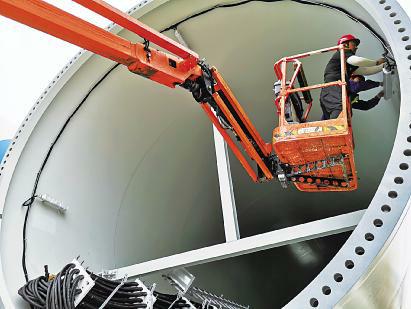
科技创新是推动企业发展的力量源泉。
回顾装备公司转型发展之路,有一个问题不容回避,那就是究竟是什么在不断推动他们在前进的道路上取得一个又一个辉煌?
早在酒泉公司刚开始陆上风电塔筒制造之时,董贵林就问过大家一个问题:“我们这样的加工企业,一没有高端的设备,二没有定型的产品,三没有雄厚的资金,靠什么去竞争和发展,在高手如林的平台上竞技,我们凭什么取胜?”
这是生存之问!
当时,在酒泉风电产业园中汇聚了22家国内国际风电装备制造企业,其中13家为上市公司,中央企业8家。这其中,除去风机、叶片厂商外,和四局一样从事塔筒制造的还有华锐风电、中材科技、中复连众等十余家重量级“大咖”。
进得去“陆上三峡”是值得庆幸的,但要立足“陆上三峡”,庆幸之后更多的是危机感和紧迫感。进得去,还得立得住,更要走得远,但设备、产品、资金等等这些,对初闯戈壁的装备人来说,都没有优势。
凭什么取胜?
“只能靠科技创新!”面对强手如林的竞争现实和企业生存的极度渴望,董贵林给出答案。
依托项目广开科研,智慧创新,以技术提效率,向科技要效益,培育核心竞争力。这,不仅为酒泉公司突出“重围”指明了方向,也为日后整个装备公司以科技创新全面打造“四局装备”品牌提供了遵循。
方向定了就是干!没人给人、没钱给钱,请人进来教、派人出去学,新技术新工艺应用、传统技术融合创新……一个科技创新的大氛围伴随着装备制造的紧张节奏协同展开。
“为强化科技研发的组织领导,酒泉公司建立了适应企业科技开发的组织机构,集中科研力量组建了企业技术研发中心和风电塔架制造工程技术研究中心,专门负责开展新产品、新工艺和新技术的研究、应用。”装备公司总工程师,时任酒泉公司总工程师的朱锴年说,“同时,还强化外部技术资源的整合,与兰州理工大学、华北水利水电学院、风电专业厂家联合,实现自主开发与‘借力’开发相结合。”
智慧与实践一结合,便是成果无数。
2010年,酒泉公司首个技术成果《提高风电塔架质量验收一次合格率》获得国家电力建设质量管理成果一等奖。此后更是成果迭出,而且分量也越来越重。《兆瓦级风力发电机组塔架规模化制造辅助设备研制与应用》《2.0兆瓦风力发电机组塔架先进制造技术及工艺的研究与应用》《低温风力发电机组塔架门框高效焊接工艺》三项成果被专家组鉴定为“国内领先水平”,《兆瓦级风电塔筒规模化制造辅助设备研制》共研制出风电塔筒多功能焊接机架、叉车转移风电塔筒单节筒体支撑架等11项性价比优良的辅助设备,填补了国内风电塔筒制造辅助设备的空白。仅仅围绕风电塔筒制造,就研制出50多个成套辅助设备。
由于成果突出,酒泉公司的技术中心被酒泉市政府认定为“企业技术研究示范中心”,同时还被确定为“酒泉市风力发电机组塔架行业工程技术研究中心”。有了地方政府的助力,更是如虎添翼。
当时,国内陆上风电蓬勃发展,但行业标准并没有统一。作为国内首个千万千瓦级的大型风电基地,甘肃省开始着手整理风电制造安装相关标准,这对国内整个风电行业都具有“标杆”意义。甘肃省质量技术监督管理局邀请酒泉公司参与编写的《风电塔架制造安装检验验收规范》(2015年正式发布),规定了陆上大型风力发电机组(风轮扫掠面积等于或大于200平方米)钢制管状塔架的制造、安装技术要求和检验方法,酒泉公司许多科技成果以行业标准的形式被确定下来,他们一跃从风电的参与者成功跻身行业规则的制订者。
而此时,距离装备人第一次“触风”的时间还不到5年。
2012年10月,酒泉公司成功通过“国家高新技术企业”认定,不仅是在酒泉风电产业园,而且是我国西北地区唯一一家获此殊荣的风电设备制造企业。
2017年8月,酒泉公司因科技成果转化为现实生产力效果突出,被甘肃省科技厅第一批授予“甘肃省技术转移示范机构”;2018年10月,酒泉公司设计中心被甘肃省工业和信息化委员会认定为“甘肃省省级企业设计中心”。
“到2018年,我们的高新技术企业证书已经经过两次换证复审,全部顺利通过。”朱锴年说,“截至目前,酒泉公司已先后获得62项国家专利、8项省部级以上科技进步奖,在整个园区首屈一指,彰显了企业雄厚的技术实力。”
依靠科技创新,酒泉公司从“零”开始,一步一个脚印,拼出了自己的品牌。而在品牌的背后,是市场规模的扩大、生产效率的提升和经济效益的增长。“在2013年整个产业园区产能开始显现饱和之际,我们的市场占有量不降反升,全年实现签约3.8亿元,创下历史最好水平。”酒泉公司总经理高治学说,“面对大环境的持续低迷,园区很多厂家已经倒闭和转产,而我们的市场份额却在持续在增长,截至目前,合同储备达17个亿,也创下了历史新高。”
科技创新带给酒泉公司的是实实在在的“甜头”。
国内很多厂商在同装备公司接触后,都愿意建立长期合作关系,就是因为他们提供的产品质量优。国内最大、世界第二的风电制造厂商金风科技有限公司将其纳为长期合作伙伴(全国仅两家),产品的科技含量是一个重要因素。
2017年,随着进军海上风电装备制造的“战鼓”擂响,科技的大旗已先于制造业务展开。在阳江公司成立之前,装备公司就已经开始着手海上风电塔筒等装备的技术准备工作,为顺利“进位”做好准备。
“阳江公司从一开始确立了科技引领的工作思路。”装备公司副总经理、阳江公司总经理张阳勇说,“海上风电装备由于受海洋特殊环境的影响,同陆上风电装备制造有很多差异,技术要求更高,科技支撑作用体现更为明显。”
2018年,随着阳江公司生产步入正轨,技术创新工作多管齐下。广泛开展“五小”创新活动,激发一线员工发明创造;实施人才培养计划,以拥有丰富的专业知识及实战经验的技术带头人一线解决技术难题,寓“传、帮、教”于实际科技创新工作;确立课题,专项研究实践技术制约难题;借助外力,联合技术攻关。
“过去两年,阳江公司在科技创新方面总共投入了1300余万元,获得10项专利授权,取得QC成果2项、工法成果2项,还有五小成果14项……”阳江公司总工程师张威介绍,“我们积极借助社会力量,开展科技研究,也取得了显著的成果。与阳江五金刀剪研究院联合成立海洋风电制造技术联合实验室,联合申报的高功率新型研发机构获得广东省专项资金支持;联合当地高校和研究院以大直径、大厚壁海上风电设备自旋转电弧窄间隙焊成套技术研发与应用,联合申报了2020年省级促进经济发展专项项目。”
就在刚刚过去的6月份,阳江公司又收到一份喜报:2019年申报的《超大直径抗台抗腐蚀型海上风电塔筒》获得广东省高新技术产品认证。这个被装备人优化了工艺的塔筒,可使它在海上的寿命延长5年。“这是我们进入广东来,获得的第一个高新技术产品认证,是对我们海上风电制造技术的充分肯定,对公司今后技术研发和市场开发都有重要的影响。”张威说,“目前,我们已经完成全国科技型中小企业信息库入库登记,下一步,将积极扩大技术研究成果,提升技术创新水准,力争今年申报国家高新技术企业,用科技为企业未来的发展增添强劲动力。”
2019年8月19日,中国海工装备制造全新一页揭开,总重421吨、高度84米、最大直径7.5米的国内最大直径海上风电塔筒正式下线;2020年6月22日,总重1567吨、直径8.1米、高度97米的粤西首套“巨无霸”海上风电单桩基础钢管桩顺利下海;2020年6月23日,单桩重190吨、最大直径4米、长40米的国内首套大直径四桩导管架基础钢管桩成功完成海上沉桩……这一项项国内海工装备制造的标志性事件,背后是科学技术的全新突破,这其中都闪耀着四局装备人智慧的火花。
“只有保持在技术领域的领先,才能在未来的市场中赢得更多的话语权。”朱锴年,这位身负53项国家专利、8项省部级科技进步奖主创者光环,被青海省政府授予“优秀专业技术人才”的装备公司科技带头人,对科技创新与企业发展的关系有着深刻的认识,“没有核心技术在手,企业走不长。”
这两年,朱锴年长期驻守装备公司在海峡西岸的福清海工装备制造基地。这里,是水电四局装备制造业的一张亮丽“新名片”,是装备公司由传统海工装备制造向高端海工装备制造升级的“桥头堡”,是企业立足高端风电制造市场技术创新的又一“制高点”。
在福清,朱锴年和他的技术团队面对的是海上风电大容量定转子支架制造的全新“课题”。
“我们目前制造的是今年3月刚中标的7兆瓦海上风电定转子支架,定子机座最大加工直径7米,加工高度1.8米;转子机座最大加工直径约7.4米,加工高度2.1米;加强盘厚度达到150毫米,最大加工直径7.4米。”朱锴年说,这个“大家伙”生产过程极其繁琐,加工难度非常大,产品精度要求极高,仅这上面的上千个螺纹孔,位置度偏差就得控制在0.3毫米以内,“这不仅需要高精度的制造设备,也需要我们精良的技术和工艺。”
为了这个“大家伙”,朱锴年已经做了近一年的准备工作,2019年上半年,他们就着手准备相关资料研究,7月份专门成立了定转子支架研制攻关小组,在接到正式订单前,研究团队先后完成了定转子支架工装设计、设备改造、工艺设计等一系列技术准备工作,并成功应用于6兆瓦风机定转子支架的试制工作,积累了宝贵的经验。
“从未来海上风电发展方向来看,机组装机容量会不断增大,结构件尺寸也会随之增大,对于配套的装备制造提出的要求也就越高,我们必须加紧相关技术研究及创新工作,在加工技术、工装研发、新工艺等方面取得一定的技术成果,创造品牌、赢得市场。”朱锴年说,“我们目前研究的领域都是海上风电的前沿技术,不仅对我们自身的发展意义重大,而且对我国引领世界风电科技水平都有着深远的影响。”
在不到一年的时间里,他们已完成9项专利申报,其中2项还是发明专利;围绕工装设计、工艺技术改进、施工方法创新形成9项成果并已付诸实践;2项QC成果已通过中国电力建设企业协会审核……福清公司的科技创新能力,给整个园区“耳目一新”的感觉,但这仅仅是个开始,后期随着定转子支架规模化生产和其他产品开发,定会有更多的“惊喜”涌现。
十年砺剑,其光如炬。在科技创新的大旗引领下,装备公司从昔日黄河之滨走向五湖四海,又踏着河西走廊的戈壁一直行进到蔚蓝大洋,技术变革犹如不竭的源泉推动装备人转型的步伐不断向前。而这种以科技为引领的发展思路,也全面渗透到装备公司传统水工产品制作、起重设备制造、钢桥梁结构加工、铁路配套设备制造、水电站运营检修和EPC总承包等多元产业体系中。
2009年,装备公司根据转型的需要,全面亮出“科技兴企”的大旗;2014年,结合发展的形势,把“提高科技创新能力”作为工作主线进一步深化;2016年,随着向海工装备的转型,进而提出把科技创新工作放在“关键位置来抓”的进一步强化;2019年,更是将科技创新提升到“品牌战略”的高度着重强调。期间,在改善科技创新环境、完善科技创新管理体系、重点技术突破、产业创新转型升级等方面制定了诸多措施,逐渐形成“依托项目、自主创新、社会辅助、产研结合、重点攻关、突出实用”的科技创新模式,多个产业领域全面开花,取得一系列丰硕成果。
特别是近五年来,装备公司组织搭台、资金支持、人才唱戏,各项科技成果呈“井喷”状态。截至2019年底,装备公司已拥有国家专利授权202件,其中发明专利8件、外观专利12件、实用新型专利182件,是水电四局二级单位中拥有国家专利数最多的一家;完成企业和省部级以上工法27部;获得省部级以上科技成果15项。取得水工金属结构产品生产许可证、特种设备(起重机械)制造许可证、特种设备(压力容器)制造许可证等多种资质,还是我国西北地区唯一一家钢结构制造特级资质企业。2016年,装备公司被授予“国家高新技术企业”,所属十个二级单位中,两家被授予“国家高新技术企业”,两家进入全国科技型中小企业信息库。
“当前,我们科技创新工作的主要思路是以自主创新为主线,坚持低成本投入、高技术含量的创新原则,重点做好基础设施、工装设备、工艺技术以及设备的研究和创新,加大核心关键技术攻关力度。以合作为辅线,积极寻求政府、院校、科研机构支持,加大科研立项,为装备公司科技研发工作争取更大的平台和支撑。”朱锴年表示,就是要通过科技创新,强化“四局装备”品牌影响力,助力装备公司成为质量效益型行业标杆。
转型发展,是传统企业“破茧重生”的必由之路。但这意味着要走一条从未走过的路,注定是一条奋起和超越的路。在这路上,没有遍地鲜花,有的只是丛生荆棘,缺乏创新的思维和变革的手段是踏不出通途的。
装备公司科技创新的实践表明:通过开展科技创新,不仅有效提升了工作效率,而且有效降低了施工成本;不仅有力提升了“四局装备”品牌的含金量,而且有力增强了企业核心实力。科技能力转化为核心实力,进而升华为竞争优势,成为开辟市场的利器,为装备公司不断发展壮大提供了源源动力。
沧海横流识本色,烘炉烈焰辨真金。身处科技进步突飞猛进的新时代,面对市场竞争优胜劣汰的新考验,如何肩负起高质量发展的新使命,企业未来的出路在哪里?
“只有不断强化科技创新,才是企业未来根本的出路。”董贵林说,“就像习总书记嘱咐的,核心技术必须要掌握在自己手中。”